The 411 of micro welding
- microweldminnesota
- Feb 23, 2022
- 4 min read
Updated: Jan 12, 2023

The top questions customers ask about micro welding
At Micro Weld, Inc. we love helping our customers optimize their laser welding projects. Precision micro welding is such a critical component for quality and product development processes! In this blog post, we’ll answer some of the most common questions our customers ask us about micro welding. We’ll share tidbits on the history of micro welding, the advantages, common applications, material types, turn-around times, and outsourcing or in-house decision-making.
Read on and learn about micro welding!

First things first:
What exactly is micro welding?
It is a welding process that joins two pieces of materials by heating the surface of each until they become liquid, which joins them together. The resulting weld is very strong and can withstand a lot of stress. This process is often used in medical devices, precision machine components, aerospace, gas, oil, and other engineering applications where high-temperature strength welds are required.
The history of micro welding
Welding: A tradition that dates back thousands of years

Welding is a very ancient technology that dates back 10,000 years ago. There are claims that man was using hot rocks to make implements and weaponries by melting them together as early as the invention of fire itself. This welding process of melting and mixing materials to make a bond became more commonplace during the Industrial Revolution.
50 years ago, metal welding was first performed in space during the Apollo-Soyuz Test Project. Special equipment was used to build a helical antenna made entirely out of metal.
Laser micro welds were developed in the early 1970s to create a technology that would allow for more accurate repair work on metal components, like airplane engines and boilers. In the eighties, scientists at the Massachusetts Institute of Technology developed a micro welding machine to weld parts together as small as one millimeter thick and with tolerances under two microns.
Micro Welding Trivia: Did you know?

Micro welds are so small that they're often invisible to the naked eye and can only be seen under a microscope
The smallest micro weld is about the size of a red blood cell, 6 to 8 micrometers
You can fit over 100 micro welds in one square millimeter
Benefits of micro welding
A few of the unique advantages of micro welding:

Precision is the number one benefit of micro welding. It is an extraordinarily precise micro welding technique because you're perfecting it under a microscope.
Micro welds are extremely small, providing a strong and durable bond without compromising on the quality or look of your finished product.
Laser micro welding is a reliable and efficient way to join metals together – even dissimilar materials, making it ideal for prototype testing such as breakthrough medical device technologies.

Common applications for laser welding
Micro welding is a process that uses heat to join two materials together for micro components. It’s frequently used for molds, dies, surgical devices, and in the aerospace, gas, oil, and automotive industries because it produces a precise and stronger bond than traditional methods while keeping heat input to a minimum.
Different types of micro lasers:
Yag lasers
Fiber lasers
Frequently Asked Questions
Can you do spot welding?

Yes! Common materials could be copper, steel and stainless. This is typically done in industrial welding applications on thin material to prevent distorting the integrity of the production part.
Do you weld dissimilar materials?
Our micro welding team is always willing to test any welding process feasibility. For example, Tungsten carbide to stainless steel is a frequently requested welding application.
Metals and materials for the perfect laser weld
Common and uncommon exotic metals

The following are some of the most commonly used metals in laser micro-welding:
Aluminum
Nitinol
Stainless
Steel
Titanium
Other unique and exotic laser welding metals include: platinum, copper, and nickel

“Is this even feasible to micro weld?”
We make the impossible possible!
We have a micro welding technique and customers often react with surprise when they hear that we are able to accomplish the complicated micro-welding job that they want.
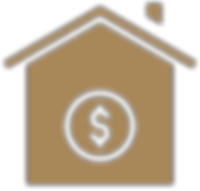
Should we tackle complex micro welding projects in-house or outsource?
The answer depends on your company’s specific needs and resources. However, what we can say for sure is that doing this type of work takes time, expertise, welding equipment, and money – four things most businesses don’t have in abundance. If you want to do micro welding well, it’s best to leave it to the experts who can help your business avoid costly mistakes and keep projects productive and running smoothly in the long run.
Expert tip: in-house projects often comes to us for rework because companies try DIY and fail.

What is your typical turn-around time for laser micro welding projects?
Need a project completed quickly? Our high precision welding team can have your project done in no time!
Micro Weld Inc.’s, typical turnaround time is one to two business days.
We also provide 24-hour emergency micro welding services. Mold revision, and repairs are frequent requests. Often times, the mold area that needs fixing is in the worst possible location (and Murphy’s Law will happen with mold failure occurring at the worst possible time).
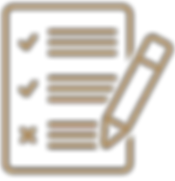
Conclusion
Whether you're looking for a micro welder consultant or ready to implement the process yourself, it's important to document your equipment needs, project goals, current quality processes and delivery timelines. We hope that our discussion of the history, benefits, and advantages will help you decide how micro welding can improve your project.
We offer free welding consultations
who can discuss your project requirements in detail and answer all of your questions so that you make an informed decision on which sourcing choice is best for your application.